Will Cox, Director, DAVISThere are so many things you have to know about working in and around a hospital. From making sure you have all precautions in place — properly installed, maintained, and inspected — to having the right mentality and the best team. That's what DAVIS brings.
Shady Grove Adventist Hospital
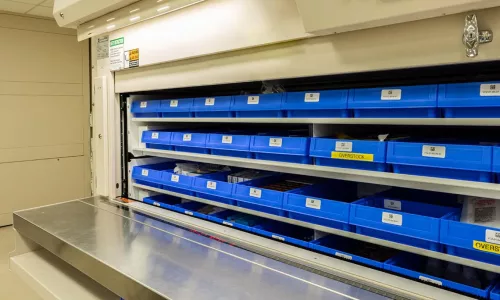
Project Brief
When we’re working in close proximity to immunocompromised patients, our team goes beyond the realm of cautiousness to approach hospital renovations with the precision of a surgeon and compassion of a nurse. That’s how we approached the multi-phased renovation (20 to be exact) of numerous occupied departments at Shady Grove Adventist Hospital (SGAH) — including particularly sensitive spaces like the Pharmacy and Centers for Advanced Wound Care & Hyperbaric Medicine.
From our project team
Critical Projects Require Complex Preparations
The SGAH pharmacy is a lifeline to the hospital. This is where raw drugs are crushed, mixed, made and dispensed — and then transferred within medically approved containers. Contamination of this air space is hazardous to the medications and poses life-threatening risks to the patients. Because of this, our phasing plan had to be exacting at every stage; finding a way to meticulously complete the work while preventing construction debris from contaminating the pharmacy. In this case, the pharmacy was renovated while remaining in operation during the entire construction process.
To do this, we built temporary Infection Control Risk Assessment (ICRA) barricades and closed off our renovation space from the remainder of the pharmacy. Once a particular section’s renovation was complete, we took down the temporary walls and repeated the process for the next section — moving section by section until the entire pharmacy was renovated. During the majority of the phases, temporary work areas such as chemo preparation were created to allow for continuous functionality of the pharmacy. Perhaps most critically, we used negative air machines to create and maintain negative pressure within our renovation area. This ICRA measure created a negative pressure environment that kept all construction dust, debris and odor within our designated work zone — preventing contamination to the adjacent, operating sterile space. Working closely with an Infection Control Supervisor, we monitored the ICRA for Healthcare Construction performance daily to ensure we were taking the proper precautions and meeting all guidelines.
Raising the Bar
In addition to the pharmacy, our work in the infusion, wound care, and adjacent sterile processing departments required the creation of similar ICRA measures. We installed two hyperbaric chambers along with all of the required mechanical and gas piping to feed the chambers for oxygen therapy. This work was meticulously planned over months to allow for a successful relocation over a weekend to minimize patient treatment downtime. Our attention to detail during this work was unmatched, as we knew that the slightest error could cause a utility disruption and put patients’ lives at risk.
Beyond these departments, we upgraded the common areas finishes, including renovating the main lobby restrooms, executive boardroom, and corridors that surround the first floor clinics and cafeteria, as well as relocating the Environmental Services Department offices. Before starting on the major project renovation areas, we built an incident command center where chief hospital executives and clinical supervisors could meet to collaborate during emergencies. In total, we completed every phase of this highly technical, highly controlled hospital renovation without disturbing SGAH’s day-to-day schedule or disrupting the people who need peace the most — the patients.
Photos by Jim Tetro
You May Also Like
See the latest projects and the people who made them possible
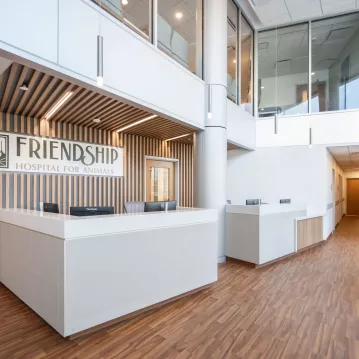
Friendship Hospital for Animals
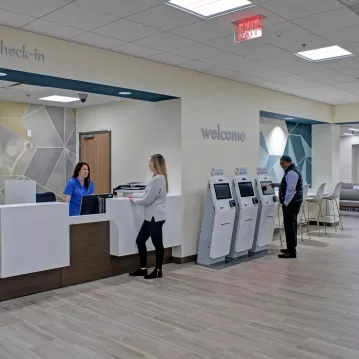
Kaiser Permanente Colonial Forge Medical Center
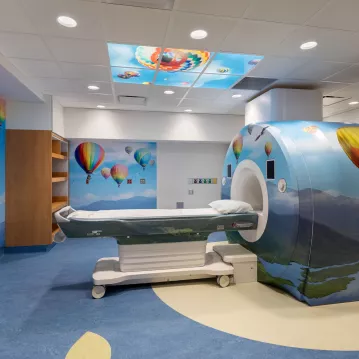
Children's National Hospital System
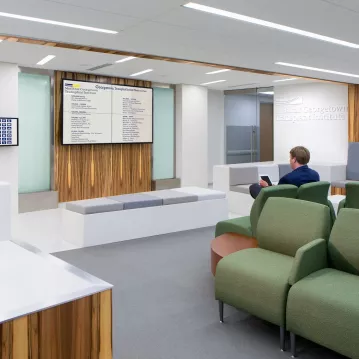
MedStar Health Hospital System
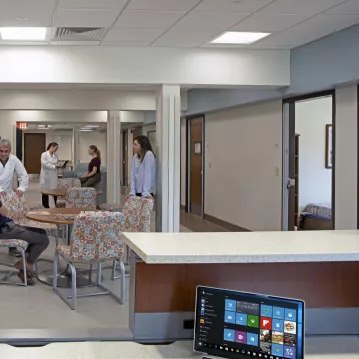
Luminis Health Behavioral Health Pavillion
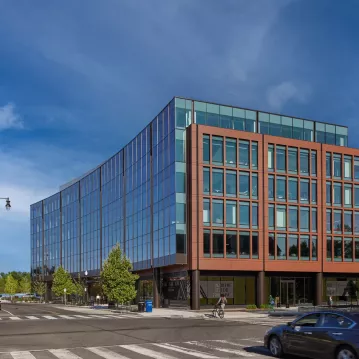